Mother
invented necessity so I just had to do something about it. This
project is for a pulse width modulated dual drill speed controller.
For driving small, low voltage, DC drills and using switch mode
topology. This is not the easiest stuff in the world to make happen
and is not recommended for the beginner. It is relatively safe to
work with but not trivial and could still be lethal if built by
an idiot. As always I take no responsibility for any misadventures
with this information. It is published purely out of interest. However
if you do get into this stuff then you're welcome to drop
me a line about it.
Desk lamp boom sporting a holster for the
drill and a 12 volt fan and housing on a gooseneck.
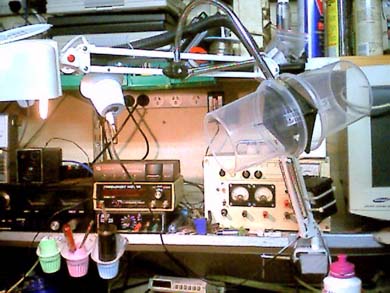
Another view showing the goose necked sucker
more clearly. Where ever the light shines there's a suck not far
behind. Note also the high speed drill in the blue holster 3rd from
the left. Attached to the bench shelf.
DEFINING THE PROBLEM: The
necessity was that I had 2 DC drills. Both of which were in need of
something better than what was driving them. Especially after a recent
bench upgrade and reorganization. It's a long story but a simple variable
linear regulator wasn't going to cut it. The problem being that the
lower the speed, the less torque the drills have. PWM (Pulse width
modulation) is ideal for this kind of work in theory but it's not
without it's problems either. One is complexity. On the surface, the
finished project looks pretty simple but it was not trivial to develop.
The chips used are UC3843s. These are fairly common SMPS (Switch Mode
Power Supply) controller chips which I acquired from a dealer on eBay.
They turned out to be not very helpful for my original intentions
and operated somewhat differently to what I had anticipated.
They
are used here, in a somewhat unusual configuration for a number
of reasons. Mainly this is because I didn't have any power MOSFETs
on hand and could only draw on a range of fairly ordinary power,
bipolar transistors. This presents two immediate problems. The chips
were designed to drive the high impedance gate of a MOSFET. Usually
a 10 ohm resistor is all that separates the output and the gate.
The chips run too hot and can fry when driving the base of a transistor
like this so the resistance had to be increased and a diode placed
in the path to protect the output from excessive current when it
tries to drive the base low.
The
second problem is that a MOSFET is generally used because of it's
extremely low Ron. On Resistance. That is to say, when the MOSFET
is switched fully on, the resistance between drain and source is
very low. These days, a fraction of an ohm is not uncommon. The
lower the equivalent on resistance means the less energy that is
wasted in heat through the transistor. They still get hot but considering
the amount of current they pass they tend to run comparatively cool.
By contrast, any given bipolar transistor will exhibit around 0.7
volts drop between collector and emitter. This translates into a
huge equivalent on resistance depending on the voltage and current
being switched. They tend to heat up rather quickly.
This
presents one of the two huge advantages of a switch mode power supply
as compared to a linear. The MOSFET is either on or off. When on
it has an extremely low resistance. When off it has as close to
an open circuit as you can get. By contrast, a linear regulator
such as the two pre-regulator circuits used in this project, use
the transistor as though it were a resistive element. As the transistor
is loaded up, the excess voltage translated into heat and is wasted.
The heat has to be dealt with and the transistors have to be much
more robust.
The
SMPS circuit used here is then, a compromise. The transistors are
either fully on or off as with a MOSFET but one has to take into
account the 0.7 volt drop of a bipolar device and deal with the
fact that it is still going to waste excessive energy in heat. Despite
this, it's still far more efficient than if it had been a linear
regulator. But this is not the main reason for using a PWM system.
A
PWM circuit has the advantage of being able to quickly translate
voltage to current as the system is loaded down. A series of pulses
are at full voltage but are integrated across an LC network. The
pulses charge a capacitor to a given value and then back off to
maintain that voltage. If the output is suddenly loaded down as
the drill bites into something, there is always the full potential
of the system to draw on to maintain it's torque.
Another
advantage is that if the capacitor is a little on the low side compared
to the loading, large, full potential spikes will pulse into the
motor. Helping to jog it free of jams. This is extremely helpful
at low speeds. Most variable speed power drills use this technique
these days. Although they run directly on Mains potential, the motors
are in fact DC. The mains is rectified and chopped up similar to
a switch mode and can deliver high torque at low revs.
Apart
from the chips themselves, this project was pretty much all built
out of salvaged parts. I should mention the other requirement of
this box too before I describe the circuit. That is, to drive some
fans which are used in an attempt to draw soldering fumes and smoke,
away from my face while soldering. As can be seen in the photos,
one of the drills and a fume sucker, are mounted from my bench lamp
boom. Where the light goes, so does this gear. There is also a pair
of mains powered muffin fans at the back of the bench to try to
draw smoke away from the work aria. So if you're wondering what
the Solid State Relay and the 12 volt fan regulator is for, this
is it. It would be safe to ignore these things if you so desired
but they are in this unit because of their commonality with the
drills and their station.
DOWN TO BUSINESS:
Because
of the above definitions, I decided to use the transistors in a
more unusual, common base mode. Rather like a series pass transistor
used to extend the current handling of a conventional linear regulator.
Except here it is turned hard on or off. But this in it self presented
a new problem.
The
UC3843s usually sense current by a small resistor placed at the
end of the switching transistor. This transistor pulls down one
end of a pulse transformer. As this transformer loads up the voltage
developed across the resistor rises. If this voltage rises to 1volt
or more, the current sense input triggers and shuts down the output
until the loading becomes more reasonable. Obviously I couldn't
do that since the transistor is now used in series pass mode. What
I could still do however is run the return path of each output through
this resistor with the trade-off being that each output can no longer
be directly ground referenced. There can be no common return path
for both drills or in common with any other I/O.
TUNING THE CURRENT:
If
this resistor is 1 ohm, the circuit will trip when the current exceeds
1amp. A bit of obvious ohms law here. Therefore for 2 amps, half
an ohm is required. I've used 0R39 in this case giving somewhere
between 3 and 4 amps which is plenty of grunt for the drills. It's
also the only suitable resistor I had. The max wattage developed
across a this resistor will be about 300mW. Which is 50mW more than
a conventional quarter watt resistor can withstand. The closest
I could find was a huge 5 watt beast. Way overkill but you can use
a half watt resistor if you have one available. Likewise you can
tune the max current to suit your application.
An
RC filter is placed between the current sense input and the current
sense resistor. This is designed to filter out any voltage spikes
that may occur during loading and adversely trigger the current
sense input. The filter is a no brainer to figure out. A 1K resistor
and a capacitor the same value as the oscillator timing capacitor
is all that is required. You can make this a little larger if you
wish but you can do it all by rule of thumb.
TUNING THE VOLTAGE:
The
output voltage is determined in a similar manner. Only here, the
threshold is 2.5 volts. The output voltage is fed back to the voltage
sense input amplifier via a potential divider. Simply put, the divider
makes sure that there is just 2.5 volts when the output voltage
is at it's desired level. For example, if you wanted a fixed 5 volt
output, you'd simply divide this in half. Say a pair of 1K resistors.
The junction of which would be 2.5 volts when the output is 5. The
chip would then try to maintain the output at 5 volts by advancing
or retarding the pulse width of the output.
To
make a variable supply one essentially replaces the potential divider
with a pot. Although some current limiting resistance seems to be
required to prevent the input comparitor/op-amp from saturating
at extremes. The only hard thing to wrap your brains around here
is that the pot works backwards to what we'd conventionally think
of with something like a volume control. The more voltage fed back,
the less the output voltage. This is the same deal as with the gain
of an op-amp and that's essentially what you're doing. Adjusting
the gain of the circuit. The minimum voltage is therefore around
2.5 volts while the maximum is limited by the supply potential.
The
reason for the two different feedback schemes is that the two drills
have differing requirements. The drill on the lamp boom has a maximum
voltage of 16 volts while the high speed PCB drill is 32. So the
former needs to be limited to 16 but with the full travel of the
pot.
|
TURNING
ON AND OFF:
I
did not wish to place a switch directly across the outputs of the
drill supplies. The switches I used came from an old commodore 128
console. They are like normal key switches but are latching. They're
not designed to handle much current. Fortunately there is a recommended
shut-down scheme for these SMPS chips. Unfortunately it tends to
drive them a little hot for some reason. I'm not entirely happy
with this but it's yet to be detrimental to the performance so I've
left it as is. This is the recommended shut-down scheme in all of
the data sheets but said data sheets tend to be a little lite-on
for facts.
You
can do one or both of these things to shut the chips down. Either
raise the current sense input above 1 volt and/or drag the COMP
pin below 2.5 volts. By placing a PNP transistor across these two
pins both may be achieved but getting this right under these conditions
was where I blew up most of the chips in development. And when I
say blew up, I mean big time sparks and smoke. At one point I swear
I saw a small mushroom cloud accompanying the rather brilliant flash
of light. In total, 4 chips went up in smoke before I figured this
out so be warned.
In
hind sight, I would probably simply put this PNP transistor between
the reference pin and the current sense pin. But NEVER put this
between any pin and the supply voltage. That was explosion number
two as I recall.
The
diode is absolutely necessary. As are the resistors on the base
of this transistor. Otherwise, you end up dumping the supply voltage
through the transistor and into the chip again and you can guess
what happens then. Only this time you'll take out the transistor
as well. Possibly even the second pre-regulator. This was explosion
number 3.
Eventually,
this scheme will leave you with a chip that's shut down until you
hit the on switch and therefore you need not pass huge currents
across the contacts of a small switch.
THE OUTPUT BITS:
The
diodes across the outputs are absolutely necessary. You can safely
ignore the diodes on the supply side of the transistors because
they were there from a previously experimental output scheme. I've
included them in the circuit because they are there in the prototype
and years later I might wonder what that was all about. But the
other two are necessary. Firstly the transistor needs to be protected
against reverse EMF from the output inductor. Secondly, and perhaps
more importantly, the capacitor needs to be protected from back
EMF from the motors and the inductance of the cabling. You can easily
fry these electros and it won't be obvious until you jam a load
on. Naturally I found out the hard way.
In
theory the inductor isn't necessary but it improves efficiency.
Simply pumping the capacitor has the problem of wasting a lot of
power overcoming the in-rush current of the cap while it's charging.
This is not a major problem if the regulator were at full steam
all the time. However at slow speed the interval between mark and
space of the PWM is relatively long and therefor spends a great
deal more time overcoming this. The inductor passes a current almost
immediately but then collapses during the space period. This is
somewhat out of phase with the over all cycle and tends to overcome
the next cycle's in-rush.
The
value of this inductor isn't critical. I used what ever I had available.
Just as long as the winding can handle the current. Initially used
a little 1uH SMD inductor. That worked OK until the first really
big load. Then it was toast. Quite literally. It turned brown and
shed crumbs.
The
switching frequency of the oscillator is around 30Khz in this case.
The faster the switching, the more efficient the conversion. It
is not uncommon to hear of SMPS systems that switch at 1 meg these
days. Though how they suppress the RF they must generate I'm not
sure. But this is why I could get away with a very small output
cap. In this case just 47uF. However if this were to be used to
drive something other than some DC motors or lamps, a much larger
cap would be recommended. As previously stated, this whole thing
was designed to allow a little bit of pulsing to get through under
extreme loads. In an attempt to jog the drill.
The
drills will in fact run with no cap at all. However this may not
be the case with any given load. At 30Khz or so, strange inductance
phenomenon may present themselves through the windings of the motors.
The motors run smoother with the caps and they help snub out any
RF that may be transmitted.
A LITTLE WORD ON PRE-REGULATION:
As
mentioned earlier, the whole thing was made with scrounged bits.
The transformer was from an old IBM terminal. When rectified it
gives out 56 volts at about 4 amps. This has to be dropped to a
voltage that everyone can deal with. Thus the pre-regulation.
The
12volt linear regulator has a maximum input voltage of 40 volts.
The SMPS chips are 30. The max supply for the drills comes in at
32. etc. But in hind sight I could have gotten away with just one
of these pre-regulators.
You
could have a single pre-reg of around 28 ~ 30 volts to supply the
fan regulator and the SMPS chips. The main output supply could have
been derived directly from the raw 56 volt supply since the output
switching transistors could have easily handled this voltage.
The
reason it ended up like this was because I started out by following
the data sheets on the SMPS chips. Which, while not actually erroneous,
are somewhat confusing and lacking in detail. It was only after
some fairly extensive research and at least one destroyed chip that
I began to figure out the real deal. And I hope I've been able to
provide some insight above. However I've also included the data
sheet which you can find here.
The
Pre-regulator to run the chips should be as close to 30 volts as
possible in this case. I'd suggest, and have indeed used, 28 volts.
This is because of the use of bipolar transistors as the switching
elements and the ability to drive them effectively. But if you do
drive them close to 30 volts, make sure there's no way it'll shoot
over that. Explosion number 4 came when the zener went open and
the pre-reg dumped 34 volts to the chip. within seconds the chip
exploded. This became a short circuit so the transistor on the pre-regulator
then exploded and as it did so, one of the darlington pairs on the
primary pre-regulator grunted and died.
So
much for the un-killable 2N3055s.
TRANSISTOR TYPES:
The
type of transistors used are not critical. Except in that they have
to withstand the conditions placed on them. The second pre-regulator
is perhaps over-kill for the amount of current it needs to deliver
but I still wound up putting a small heat sink on it. Those SMPS
chips do draw a fair bit of current in this configuration.
They
get warm because they are running quite near their maximum supply
voltage and they are having to drive a load for which they were
not entirely designed for. Coupled with the factthat the shut-down
scheme isn't entirely as efficient as it perhaps could be, means
that the pre-regulator transistor needs to be able to supply a bit
of grunt.
I
used a pair of 2N3055s because I figured it was way over-kill. But
despite that, I still managed to kill one of them. The sound it
made when it blew was worth the price of admission though. It kind
of squeaked, then grunted and finally popped. Rather like a heavy
metal breakfast cereal I guess. I only wish I could have recorded
it. But you may hear some artifacts from the coil at low revs and
high torque. Cute littlesound that it is. My battery drill makes
a very similar sound under the same conditions and I always wondered
what that was.
THE WAFFLE AT THE END:
Once
again. If you have any queries or think I've missed something out
then I'd be happy to try and help you out. Just so long as you don't
send me brainless dialog. Contact details can be found
here.
If
you kill, maim or injure yourself, or others, I don't want to know
about it. This project represents what I did to achieve a goal and
what you do with that information is entirely yourproblem.
There
is no PCB for this project. I had considered designing one but realized
that everyone's requirements would be different. I'm sure most people
will use this article as something of a template rather than a direct
construction blueprint and the transistors chosen will be different.
However if enough people wanted boards I might consider designing
one. Maybe even making them if so required.
BABBLE-O-GRAPHY & ACKNOWLEDGEMENTS:
I'd
like to thank both Eric Barbour of Metasonix fame, and Paul Perry
of Frostwave fame for their invaluable help in developing this project.
Without whom this would never have been possible. These guys make
musical/audio gear that is both unique and second to none on this
planet. Or any other planet as far as I know. Though I only know
of a few dozen planets within a few thousand light years of here
that are even into music. And most of them are limited to banging
rocks together and hitting each other.
I'd
also like to acknowledge the following sources of information on
the subject which are highly recommended.
Switching-Mode
Power Supply Design
http://www.smpstech.com/
LAZAR's
POWER ELECTRONICS CORNER
http://www.smps.us/
QRP
FOR YOU
http://www.qrp4u.de/index_en.html
HISTORY
AND DEVELOPMENT OF SWITCHED-MODE POWER SUPPLIES PRE 1987
http://www.steve-w.dircon.co.uk/fleadh/mphil/history.htm
dc-dc
converters, switching mode power supply, power electronics, Pspice
http://encon.fke.utm.my/nikd/dcconverter.htm
AND FINALLY, SOME PORN SHOTS:
Be absolutely Icebox. |